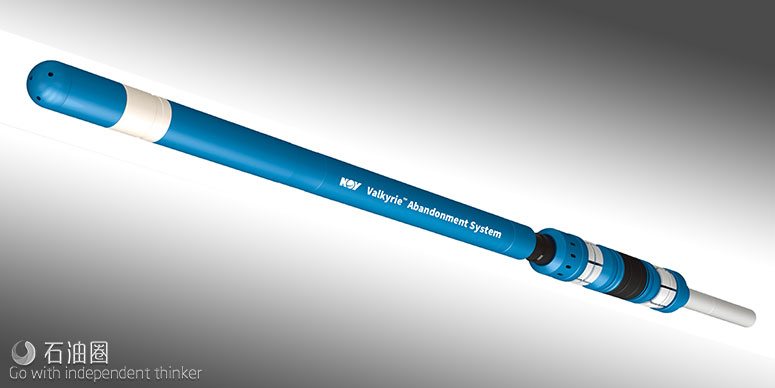
Valkyrie弃井系统,可形成一层高质量永久防护屏障。
来自 | NOV
编译 | 白小明 影子
封井、弃井作业涉及一些清除和处理油套管的难题,这些困难无疑将增加作业成本。采用磨铣作业不仅耗时而且还需钻机配合,另外如果封井时形成的环空水泥胶结质量太差,则无法形成稳固的屏障。国民油井华高(NOV)的Valkyrie弃井系统,通过轴向和侧向的振动来提高水泥覆盖面积,可以形成一个永久的防护屏障,建立一个环境安全的优质的胶结面。
Valkyrie弃井系统属于一套综合弃井策略的一部分,该策略可以帮助用户安全、高效地完成弃井作业。工具使用高频液压脉冲,通过振动自由悬挂的生产油管,在环空连续传输水泥。在实验室进行的水泥样品测试确认,通过Valkyrie弃井系统泵送提高了水泥的流变性,该方案被证实可以带来更高质量的水泥胶结面,减少窜槽和微环隙的形成。使用Valkyrie弃井系统后,用户可以减少从一口井回收的套管数量,利于环境保护,而且在不牺牲井筒压力完整性的情况下实现成本最小化。
系统采用电缆及一个会被废弃的封隔器下入,使用高频液压脉冲来活动自由悬挂的生产油管,并连续传输环空中的水泥。工具通过振动油管来提高固井作业质量,尤其是在油管靠在井眼底边的区域。通过在泵送的同时使油管运动,系统减少了微环隙的形成,从而完成一次次更稳定、更永久的弃井作业。
通过减少单井必须回收的套管数量,系统在不牺牲井筒压力完整性的情况下实现成本最小化,提高了封井&弃井作业的效率。
优势
1.创新的设计—基于公司行业领先的Agitator系统,该系统已在全球使用超过50,000次;
2.改善的流变性—经过实验室测试及现场使用验证,系统改善了水泥的流变性;
3.更高的水泥胶结质量—水泥分布更均匀,减少窜槽和微环隙的形成。
技术参数
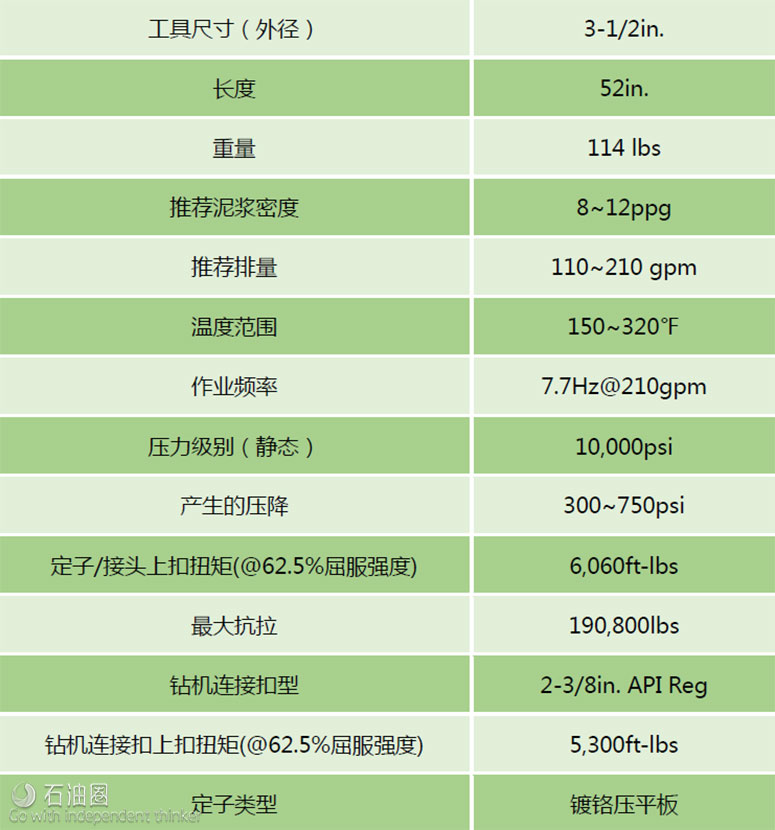
案例研究
在位于其阿伯丁的评价中心,一家作业公司在一个测试井筒进行了试验。钻机测试的目的是评估轴向和侧向的油管振动,振动主要通过采用弃井系统泵送一种属性与水泥类似的体而形成。在试验过程中,该井采用了975m的9-5/8in.套管并在其内下入了5-1/2in.油管,以模拟公司将来实际需要作业地区井身结构中的生产油管。采用来自NOV的Valkyrie弃井系统、封隔器总成以及BlackBox数据传感器,作业公司以不同排量测试了密度介于14.5~15.4ppg的流体。最终公司认为NOV弃井系统形成的压力脉冲使油管产生了明显的运动。虽然侧向振动级别从305~610m逐渐减弱,但仍足够使油管产生振动。压力脉冲的级别、振动的加速度和频率是排量的函数。振动的频率对于水泥的驱替效果比侧向加速度更明显。
作业公司将设备安装在了液流闭环系统中,以利于水泥的循环,从而可以在水泥通过系统后测试水泥的质量。水泥测试确认弃井系统形成的脉冲改善了水泥的属性。通过弃井系统,公司总共泵入了20bbl密度为16ppg的水泥,排量为145gpm,每隔1分钟取样一次,共取得5个水泥样本,然后将其与未通过该系统的样品进行对比。
经一家独立的实验室机构确认,引入弃井系统后的样品的流变性得到了改善。
截至目前,系统已使用了11口井,泵送的水泥量一口井比一口井多,最大井斜达到30°。经水泥胶结测井核实,总共945m的泵入段,792m井段固井质量良好。公司已经开始在更多井使用该工艺,从而将更多的油套管段留在井内。
实验室水泥样本分析已经确认,泵送的水泥经过NOV弃井系统后,流变性得到改善,从而可以带来更高质量的水泥胶结面,减少窜槽和微环隙的形成。该技术已使作业公司将多达9144m的生产油管永久地留在了井内,避免了上提、运输、清理和处理油管的相关费用。
您也有让人挠头的难题需要解决,或是优质技术想要找应用市场吗?如果有的话,欢迎联系小编微信或邮箱,也许能找到一剂良药。
二丫:131-3255-0596;zhanglingyu@raiborn.com
大安:131-3203-1392;lishian@raiborn.com
For English, Please click here (展开/收缩)
Plug and abandonment (P&A) operations lead to challenges removing and disposing of casing and tubing, which increases operational costs. Time-consuming milling may require the use of a rig, and plugging using poor annular cement might not provide an adequate barrier. Cementing solutions such as the Valkyrie abandonment system from National Oilwell Varco (NOV) improve cement coverage through axial and lateral oscillation to create a permanent, protective barrier, establishing an improved bond that is safe for the environment.
The Valkyrie abandonment system is part of a comprehensive well abandonment strategy that can help you safely and efficiently abandon a well. Using high-frequency hydraulic pulses, the tool vibrates free-hanging production tubing to consistently propagate cement around the annulus. Cement samples tested in the lab have confirmed that pumping cement through the Valkyrie abandonment system improves its rheology, and this solution has been proven to provide higher quality cement bonds, minimizing channeling and microannulus development. With the Valkyrie abandonment system, you can reduce the amount of pipe that must be retrieved from the well, create a positive environmental impact, and minimize costs without sacrificing the integrity of the abandoned well.
Deployed by wireline along with the packer as a sacrificial assembly, the system uses high-frequency hydraulic pulses to move free-hanging production tubing and consistently propagate cement around the annulus. The device oscillates the tubing to improve cement jobs, especially in areas where the tubing rests on the low side of the hole. By creating movement of tubing while pumping, the system reduces the phoneme of microannuli and helps create a more robust, permanent abandonment.
By reducing the amount of pipe that must be retrieved from the well, the system helps minimize abandonment costs without sacrificing the integrity of the abandoned well, increasing the efficiency of P&A operations.
Benefits
1.Innovative design – Based on our industry-leading Agitator? systems that have been used more than 50,000 times around the world;
2.Improved rheology – Lab-tested and proven to improve cement rheology;
3.Higher quality cement bonds – Better propagation of cement, minimizing channeling and microannulus development.
Case study
An operator performed a trial run at an evaluation center in a test borehole in Aberdeen. The rig test objective was to assess the axial and lateral tubing movement generated by pumping a fluid with similar properties to cement through the abandonment system. In the test procedure the operator configured the test well with 975 m (3,200 ft) of 95?8-in. casing and installed the 5-in. tubing to simulate production tubing similar to the well profile it intended to abandon. Using the Valkyrie abandonment system, packer assembly and BlackBox data sensors from NOV, the operator tested with varying flow rates and fluid densities between 14.5 parts per gallon (ppg) and 15.4 ppg. The operator concluded that the pressure pulses created by NOV’s abandonment system generated significant movement of the tubing. Cement displacement propagated past 610 m (2,000 ft) above the device. The lateral vibration magnitude attenuated from 305 m (1,000 ft) to 610 m, but it was sufficient to vibrate the tubing within maximum lateral restriction. The magnitude of the pressure pulses, acceleration and frequency of vibration were functions of flow rate. The frequency of the vibration had a more significant effect on the displacement than lateral acceleration.
The operator installed the device into a flow loop to facilitate cement circulation for the purpose of testing the cement quality after passing through the system. The cement testing confirmed that the abandonment system generated pulses that improved the cement properties. The operator pumped 20 bbl of 16-ppg cement through the abandonment system at a flow rate of 145 gal/min and collected five cement samples at one-minute intervals, comparing them with samples of the same cement that did not pass through the system.
An independent laboratory confirmed that rheology samples taken after the introduction of the abandonment system were improved.
To date, the system has been installed on 11 wells, with the volume of pumped cement increasing from job to job and in wells with up to a 30-degree inclination. Cement bond logs verified the results of 792 m (2,600 ft) of good cement out of 945 m (3,100 ft) pumped. The company has begun to use multiple installations of this process to leave additional sections of tubulars in the well.
Cement samples tested in the laboratory have confirmed that pumping cement through the NOV abandonment system improves rheology, allowing it to provide higher quality cement bonds and minimizing channeling and microannulus development. The technology has enabled operators to leave more than 9,144 m (30,000 ft) of production tubing permanently in the wellbore, eliminating the expense of pulling, transportation, cleaning and disposal.
未经允许,不得转载本站任何文章: