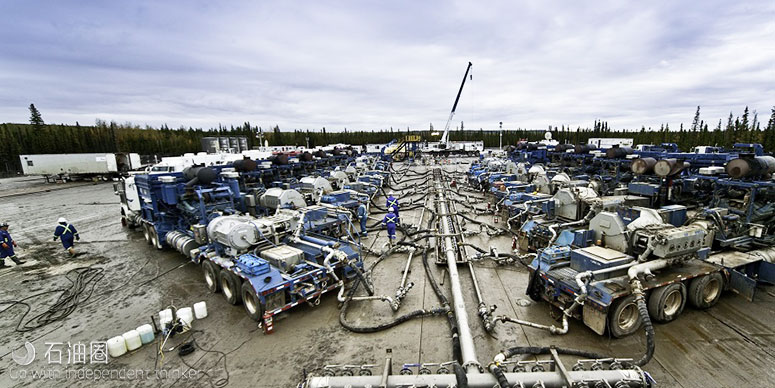
Packers Plus公司推出了全新的小井眼增产作业系统,可有效满足开发商对废弃井、成熟油藏进一步开发的需求,高效、稳定,为油气深度开采提供新的机遇。
来自 | Packers Plus
编译 | 张德凯 影子
Packers Plus公司又为其StackFRAC系列添加了新成员—StackFRAC HD Slimhole小井眼增产系统。Slimhole以小外径尾管为工具,使垂直井/斜井重复增产作业过程中工具下入更加简单,是油井重复增产、恢复停产井等作业最具性价比的执行方案。
Slimhole 以StackFRAC HD多级完井系统为基础,具有其所有的应用优势,同时兼具高效性。Slimhole这一创新性的成果使得连续泵操作过程中的增产精确操控成为可能,能够为开发商节约大量成本和作业时间。
StackFRAC Slimhole系统特性与优势:
1.以StackFRAC HD技术为基础,可靠、稳定;
2.连续泵注操作,无需钻机支持,大幅降低完井成本和时间;
3.可针对每一级压裂段的状况定制化增产方案,效率更高;
4.增产作业之后产量迅速增加,效果明显。
在多种作业中StackFRAC Slimhole系统都可发挥作用:
1.二次增产作业,包括尾管水泥固井或裸眼多级完井的垂直井/水平井;
2.FracPORT套筒可与现存油气流动口对接,建立井筒与油藏的连接;
3.停产井恢复,包括由于某些故障导致井筒完整性降低、无法进行增产作业的井筒;
4.FracPORT套筒可与现存/新射孔段建立连接,提高井筒与油藏的连通性;
5.RockSEAL封隔器可用于封堵破裂尾管段,进而可以进行增产作业;
6.进行现有水平井裸眼分支井钻井,进一步开发漏采油气甜点/枯竭区块,提高井筒产率;
7.具有停产井恢复功能,避免了新井的钻探、套管完井工作,节约成本;
8.消除额外钻井作业的次数,降低成本;
9.工具可轻松通过大狗腿度井段,安全系数高。
StackFRAC Slimhole系统构成
FracPORT H2 套筒
FracPORT H2套筒是一个通过投球或液压驱动的液体注入/油气生产端口,一般安装于RockSEAL H2封隔器之间,用于特定井段的隔离或选择性增产。FracPORT H2具有比尾管更大的流动面积,可用于保持增产作业中流体的无限制流动。此外,FracPORT H2还有“钻井开关”模式,即可根据后期作业安排调整为开启或关闭状态,对于水/气流动阻断、流量控制、二次压裂和生产测试都非常有效。
RockSEAL H2封隔器
RockSEAL H2是一种液压坐封机械封隔器,具有对称设计,同时结合了高级密封技术,确保增产作业阶段和井筒生产周期内隔离区域的高压密封性能。RockSEAL H2具有长度短、外径最小化、无需预置等特性,安装非常简便。同时,通过液压可实现精准的封隔器坐封,节约操作时间,降低成本。
案例研究1
Triassic Doig油藏位于加拿大Alberta省西北部,延伸到英属哥伦比亚省东北部。Doig油藏主要由砂泥岩、页岩构成,同时部分区块与Montney油藏重叠。Doig油藏最大厚度达到190米(623in),位于加拿大落基山脉的丘陵地带,之后向北和东的方向逐渐变薄。在英属哥伦比亚省东北部,Doig是Inga地区的主要油气产区,其油藏厚度约为25~30米。据估计,该地区油藏的每个横向截面都含有12 Bcf天然气和400万桶凝析油,Doig油藏的这种特性使得水平井和多级压裂技术成为主要开采方案。
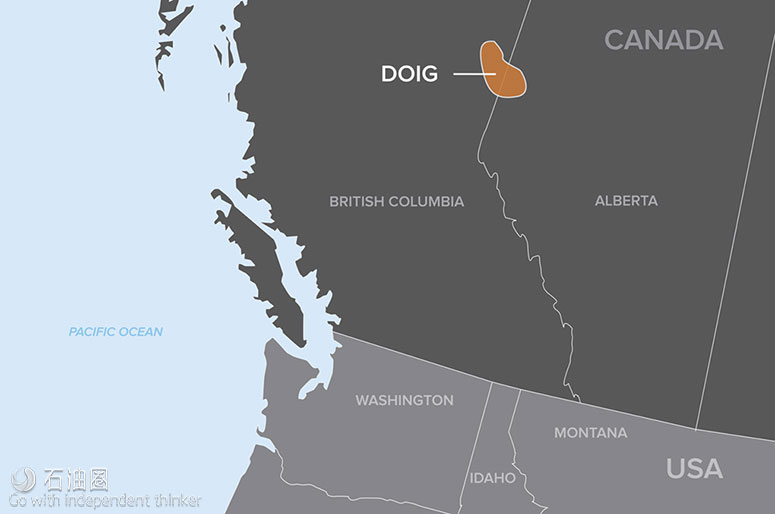
Doig油藏烦人一家开发商计划用裸眼系统在Inga地区进行一口11级压裂井的完井工作。该开发商顺利的完成了前六级压裂作业,但随着尾管封隔器完整性降低,作业遇到困难,后续的压裂作业无法顺利进行。尽管该开发商最初选择了其他服务商的完井系统,但遇到该问题后,转向Packers Plus寻求有效解决方案,帮助完成接下来的压裂作业。
该开发商首先将StackFRAC Slimhole多级压裂系统安装在井下裸眼尾管内,恢复了前5级压裂的产能。Packers Plus公司的Slimhole系统具有StackFRAC系统的所有优异性能,更专注于小尺寸尾管中的应用,例如在本案例中,使用Slimhole系统通过尾管进入井筒。
此次作业使用的Slimhole尺寸为4.5in*2.875 in,基础为RockSEAL? ll封隔器,同时配备了用于尾管内部隔离的配件。在Slimhole打破、通过尾管封隔器时,其上、下分别由RockSEAL llS矛式封隔器和RockSEAL ll封隔器协助保持密封,确保作业过程中环空的密封性能。随后,在压裂工具重新下入井筒前,用于封堵前5级射孔段的密封球被磨铣去除,恢复了井筒与油藏的连通性。
在工具安装过程中,FracPORT套筒与射孔段完成了精准对接。至此,恢复工作都已就绪,所有工具都已成功安装,即可进行剩余6级压裂作业。随后,通过丙烷压裂,完成了压裂作业。StackFRAC Slimhole是一种多功能的作业手段,对于完井作业和停产井恢复都非常有效。具体功能包括:裸眼水平井分支井钻探,发现新的油气甜点或是连接现有产层;尾管固井段或裸眼井的二次增产作业,进一步开发坍塌油藏或是枯竭油藏;对由于套管完整性低而不能进行增产处理的尾管固井井筒,可进行重新完井作业。
案例研究2
许多开发商都希望能进一步开发成熟油藏的老井,最大限度地提高油田的产量,要实现这一目标难度很大,但并非不可行。新兴的油气开采技术能够帮开发商实现这一目标,如多级压裂系统。加拿大Alberta省中部的一家开发商希望通过重复压裂技术,提高Glauconite油藏区块的水平、套管井产能。
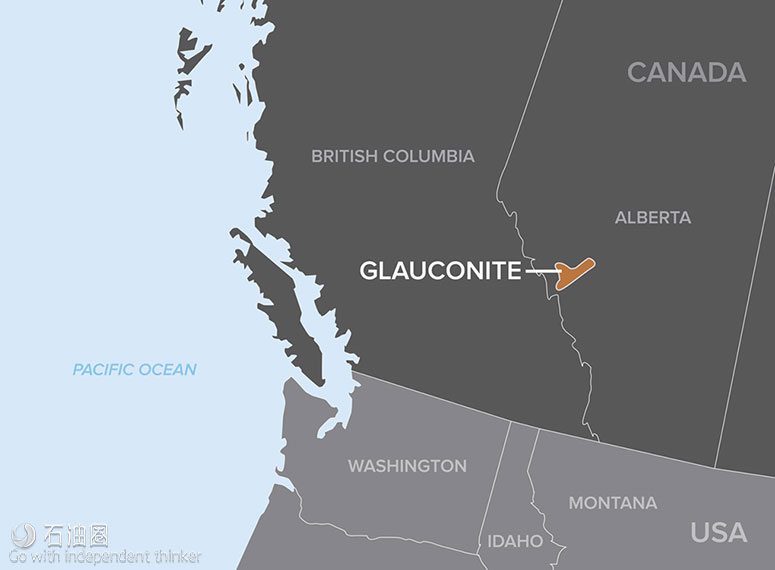
该井已经持续开采了10多年,全井筒为套管水泥固井,套管规格为4.5in,17.26kg/m L-80,最初的压裂方案产生了三个射孔段,其中两个间距约100m,另外一个位于长约900m的水平分支井内。为了以最佳效果完成重复增产作业,开发商希望在水平段对未射孔段进行压裂作业,使裂缝簇覆盖整个水平分支井。若要高效的完成此次压裂作业,目标井段压裂作业需要的转向技术和现存射孔段的生产方式是影响结果的关键因素。
PackerPlus推荐了四级StackFRAC Slimhole增产系统,尾管尺寸2.875in,可通过井筒中4.5in套管进入目标井段作业。最终,在水平段完成了3级压裂作业,其中第一级位于水平段尾部,另外三级裂缝簇间隔150~300m(包括已有裂缝簇),沿水平井方向分布。FracPORT套筒用于建立裂缝簇(新/旧)与井筒的连接,提高油藏与井筒连通性。
Slimhole系统工具下入套管井预定深度过程非常顺利,地面压力表显示,所有的FracPORT套筒都成功激活,在一天之内就成功的将100吨支撑剂下入三级压裂段内。投入生产后,除去反排期,该井最初三个月的产量达到1,900 mcf/d以上,产率相当于作业前的50倍,产量是初次投入生产前三个月产量的4倍。一年内,StackFRAC系统进行的重复增产作业总计提高天然气产量43.5万mcf。该结果充分验证了StackFRAC系统在套管水平井二次增产作业中的效果,这无疑为开发商提高未开发甜点、成熟油藏带来了新的机遇。
您也有让人挠头的难题需要解决,或是优质技术想要找应用市场吗?如果有的话,欢迎联系小编微信或邮箱,也许能找到一剂良药。
二丫:131-3255-0596;zhanglingyu@raiborn.com
大安:131-3203-1392;lishian@raiborn.com
For English, Please click here (展开/收缩)
The Packers Plus StackFRAC? HD Slimhole system is specially designed with a smaller liner outside diameter (OD), enabling operators to re-enter vertical or horizontal wells. This system provides a cost-effective solution for restimulation and well recovery applications.
The Slimhole system was developed with the same features and efficiencies as the Packers Plus StackFRAC HD multi-stage completion system. This innovative system allows for exact placement of stimulation treatments in one continuous pumping operation, saving operators time and money.
The StackFRAC Slimhole system offers many features and benefits:
–Built on StackFRAC HD technology
–Continuous rigless pumping operation reduces completion time and cost
–Custom stimulation for each stage of a previously completed wellbore|
–Immediate flowback after stimulation
The StackFRAC Slimhole system can be used in many applications:
–Restimulation of existing vertical or horizontal wells completed with cemented liner or open hole multi-stage systems (OHMS) to improve recovery from damaged or depleted zones
–FracPORT sleeves can be aligned with existing ports to establish communication with the reservoir
–Recovery of wells where a loss of integrity has hindered the ability to stimulate
–FracPORT sleeves can be aligned with new or existing perforations to establish communication with the reservoir
–Field-proven RockSEAL packers isolate liner breaches enabling stimulation of the well
–Stimulation of open hole laterals drilled off of existing verticals to exploit new or depleted zones and increase productivity
–Saves on well construction costs associated with drilling and casing a new wellbore
–Eliminates the need to drill additional wells to exploit a reservoir
–Easily installed through high degree build sections
What the StackFRAC Slimhole system is made of
FracPORT H2 Sleeve
The FracPORT H2 sleeve is a ball-actuated, hydraulically activated injection/production port. This sleeve is run between two RockSEAL H2 packers to allow specific zones of the wellbore to be isolated and selectively stimulated. By providing a flow area greater than the liner, the FracPORT H2 sleeve provides unrestricted flow for stimulation treatments. The FracPORT H2 sleeve is also available in a Drillable Closeable (DC) version that can be closed or re-opened for future operations. This allows for effective water or gas shutoff, flow control, re-fracturing and production testing.
RockSEAL H2 Packer
The RockSEAL H2 packer is a hydraulically set, mechanical packer. The dual-element design, along with premium seal technology, ensures reliable high-pressure zonal isolation during stimulation and throughout the life of the well. The RockSEAL H2 packer offers ease of installation through its short length, minimum outside diameter and anti-preset features. Hydraulic activation allows for precise control over the setting operation, resulting in time and cost efficiencies.
Case Study 1
The Triassic Doig formation is located in northwest Alberta and stretches across the border to northeast British Columbia. The Doig is composed of siltstone and shale and overlies the Montney formation. A maximum thickness of 190 m (623 ft) is reached in the foothills of the Canadian Rockies and thins out towards the north and east. In northeast British Columbia, the Doig is the main producing interval of the Inga operating area. The reservoir is 25 to 30 m (82 to 98 ft) thick and contains an estimated 12 Bcf of gas and 4 million bbl of condensate in place per section of land. Reservoir characteristics make the Doig a prime candidate for horizontal drilling and multi-stage fracturing techniques.
A junior operator targeting the Doig formation in the Inga operational area planned to complete their 11-stage well using an open hole system. The operator was able to successfully stimulate the first six stages, but encountered operational difficulties due to a loss of integrity in the liner hanger packer, which prevented treatment of the remaining stages. Despite the original completion system being supplied by a competitor, the operator approached Packers Plus for an effective solution to recover the well that would allow them to successfully stimulate the remaining stages.
The operator chose to recover the remaining stages in the well with a 5-stage Packers Plus StackFRAC? Slimhole multi-stage fracturing system by installing it inside the existing open hole liner (Figure 1). The Slimhole system was developed with the same function as the field-proven StackFRAC system, but was specifically designed for applications that require a smaller liner outside diameter, such as re-entry into existing wells.
The 4.5 in. x 2.875 in. Slimhole system was designed with RockSEAL? ll packers equipped with elements engineered to provide effective isolation inside a liner. The breach at the existing liner hanger packer was flanked by a RockSEAL llS anchor packer above and RockSEAL ll packer below the damaged tool to achieve annular isolation. Prior to re-entry, the last five ball seats in the existing open hole system were milled out and perforations were created to allow for communication with the formation. During installation, FracPORT? sleeves were precisely aligned with the perforations, enabling the remaining stages to be stimulated. After the successful installation, the well was stimulated with a propane fracture treatment. The StackFRAC Slimhole system has multiple applications for operators working in formations which require completion and well recovery solutions. These include stimulation of open hole laterals drilled off of existing vertical wells to exploit new or existing producing zones; re-stimulation of existing cemented liner or open hole wells to improve recovery from damaged or depleted zones; and re-completion of cemented liner completed wells where a loss of casing integrity has hindered stimulation.
Case Study
Many operators are looking to increase production from older wells in mature reservoirs to maximize field recovery. A key strategy to accomplish this is to leverage new technology, such as multi-stage fracturing systems. An operator working in central Alberta was interested in re-stimulating a horizontal, cased hole well targeting the Glauconite formation of the Lower Cretaceous Mannville Group.
The well was over 10 years old and was originally completed with 4.5-in., 17.26 kg/m L-80 casing cemented to surface. There were two existing sets of perforation clusters from the initial stimulation treatment approximately 100 m (328 ft) apart, a third of the way into the 900 m (2,953 ft) lateral. To maximize the re-stimulation of this well, the operator wanted to shoot new perforation clusters to cover the entire lateral. Effective stimulation of these clusters would require a diversion method that would allow stimulation of the new perforation zones, as well as the ability produce from the existing perforations.
The solution involved designing a 4-stage StackFRAC? Slimhole system using a 2.875-in. liner to re-enter the original 4.5-in. cemented casing. Three new sets of perf clusters were shot approximately 150 to 300 m (492 to 984 ft) apart along the horizontal. FracPORT? sleeves were strategically placed for targeted fracture through the new perforations as well as to allow for production from the existing perforations. The system design included a Pump Out Plug and a RockSEAL? IIS packer, which provided added anchoring to frac out the perforation cluster located at the toe (Stage 1). The next three stages used two RockSEAL II packers and three FracPORT sleeves: two located at the same depth as the new perforations (Stage 2 and 4) and one set in the middle of the two existing sets of perforations (Stage 3). The StackFRAC Liner Hanger Packer served to isolate the top of the fourth stage.
The tools were run into the cased hole to the designed depth without incident. All FracPORT sleeves opened, demonstrated by spikes in the surface pressure gauge, and approximately 100 tonnes (220,462 lb) of proppant were successfully placed in the three treatment stages in one day. The initial 3-month production rate, not including the flowback period, was over 1,900 mcf/d. This equates to an increase of over 50 times the pre-frac rate and over 4 times the 3- month IP obtained from the original completion (Figure 1). In one year, re-stimulation with the StackFRAC system resulted in over 435,000 mcf of additional gas. These results demonstrate the utility of the Packers Plus StackFRAC system to increase production rates from previously completed, cased hole horizontal wells. This gives operators the opportunity to access untapped reserves to maximize their recovery from mature fields.
未经允许,不得转载本站任何文章: