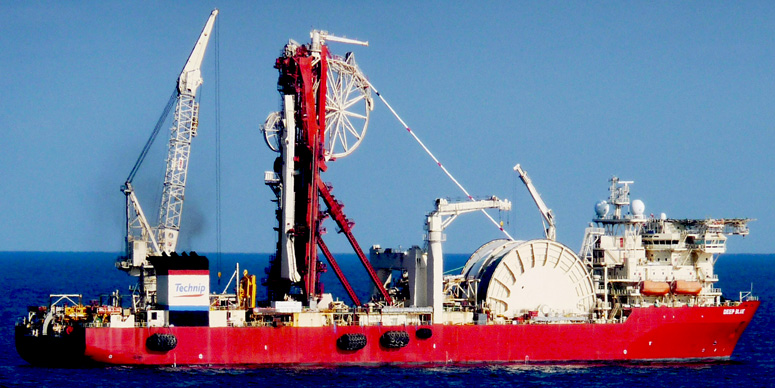
由于海上维修作业损失的生产时间,相当于每天数百万美元的收入损失。为了避免出现这种状况,研究出了对于管线的“实时”修复技术,即不需要任何停机时间的修复作业,这对于运营商来说是颇具吸引力的一个选择,并且由于其自身相当高的灵活性和运营支出效率,该技术常常得到运营商的偏爱。然而,该操作在技术上却具有一定的挑战性。
在设计时海底管线的寿命一般为20年以上,但一些不可预知的损坏往往使他们达不到设计的最佳寿命。海底油气管道的损坏可能发生在安装或者操作过程中。2015年3月公布的海底管道及海上立管泄漏修复报告(PARLOC)中,提出了从2001年至2012年这12年间,发生在英国大陆架(UKCS)海底管道和海上立管的泄漏修复事件。在PARLOC报告中提到的183件泄露事件,有160件发生在操作过程中。据PARLOC报告称,由于缺少匿名数据,无法获得所有泄漏事件的完整描述。这些统计信息在世界其它地方可能不尽相同,但尽管如此,它还是突出了海上设备完整性的重要性,以及在发生管道泄漏时采取最新修复技术的必要性。
在操作过程中,管道损坏可能由管道内外部腐蚀、氢致应力裂纹(HISC)和环境因素造成的,例如与海底管道损坏相关的不稳定的海底条件或地震,以及第三方的影响,如锚和其它掉落的物体。损坏的风险由诸多因素共同决定,但一些典型的因素包括管道设计、环境条件以及人类在附近的活动强度。如果海底管道修复作业涉及到生产平台隔离甲板部分,那么其他后勤方面的问题也同样适用。
管道的损坏程度由轻微到严重变形或断裂不等,其损坏的程度同时决定了在修复管道时所需要采取的方案。由于生产时间损失将对运营成本产生影响,因此对于发生大面积损坏的管道,修复工作通常仅限于利用带压开孔和旁路技术来切割和更换。对于大多数只是发生局部损坏的管道,诸如管道外部或内部腐蚀、局部范围机械性损伤(例如凹痕,皱褶,变形或环焊缝缺陷),那些对生产时间影响很小或没有影响的修复方法是可行的。这些修复方法被统称为“实时”修复。
多数海底管线修复技术都会涉及到一些借助机械手段或者焊接联接管线的配件,例如联轴器、钳夹、T型分支连接等。在管道修复过程中,隔离塞用于防止内部流体和海水填充管道排空的空间。再考虑一些后勤作业,海底管道修复作业具有一定的挑战性并且成本颇高。通常,大多数的浅水管道修复(挪威海域水深180米/591英尺)一直由潜水员进行。在更深的水域,管道修复必须通过远程控制技术进行。如果想获得掌握这些技术和设备资质,则需要深入了解管道设计参数和具备丰富的操作经验。迄今为止,关于深水和超深水管道修复方法仍具有很低的可选择性。
过去的几十年里,DNV GL集团在一些管道维修项目中一直担任着独立技术顾问,目标是使得“实时”管道修复不影响安全性和完整性。该公司已经开发了许多实用修复程序以及一系列“实时”修复方案。这些方案包括在管道中阻塞并注入堵漏材料对管道夹具进行修理,并对泄漏管线、注入堵漏材料的套管、管道三通用于气体容器的裂缝套管和支座进行焊接修理。
DNV GL集团负责170项世界主要的海上标准和推荐规程(RPS)的修订,目前,该集团正在通过快速联合工业项目(JIP)更新其海底管道修复的一项主要RPS,即DNV-RP-F113。 RP作为参考,广泛用于海底管道和接口的维修/修改的配件质量鉴定中。该参考指南包含这些配件和系统的设计、制造、安装和操作方面。然而,RP最新版本公布于八年前,从那时起多项新技术都得到了发展。该新JIP旨在从管道维修设备和工具的主供应商和操作人员那里获取最新最佳方法、经验和专业知识,同时将海底管道维修标准和程序规范化,成为国际公认的标准。
在海底管道方面,RP的最新版本将与海洋标准的最新版本(即DNV-OS-F101)进行统一。并且将继续扩大到能够进行修复作业的范围,包括外包管和内衬管的修复、管道表面的恢复、损害评估,既定管道损伤缓解和修复的方法进行选择以及对管道维修作业生命周期的管理。
新版本还将对安全(包括甲板和陆地部分)和与阻碍海底管线维修的有关理论提供指导,并会对管道铺设后的椭圆度和修复作业后的测试需求提供进一步的帮助。
其他改进后的设计和资格指南与管道隔离塞、酸性环境、高温/高压(HT/HP)管道修复、弹性密封件的寿命性能以及涂层去除工具对管道表面影响的验收标准等内容有关。它还将在高压焊接、对服役管道进行焊接爆裂极限检查以及像去除纵向焊缝等安装方面用于更新准则和验收标准。
Loss of production time due to repair operations offshore can equate to millions of dollars per day in lost revenue. As a result, pipeline “live” repair, i.e. repair operations without any downtime, is an attractive option for operators, and is often preferred since it yields considerable flexibility and is highly opex-efficient. It is however, technically challenging.
Offshore pipelines are designed to last for more than 20 years, but damage can prevent them from reaching their optimal design life. Damage to oil and gas pipelines can occur during installation or during the operational stages. The Pipeline and Riser Loss of Containment (PARLOC) report published in March 2015 presents loss of containment incidents that occurred on pipelines and risers on the UK continental shelf (UKCS) during the 12-year period 2001 to 2012. The PARLOC report mentions 183 loss of containment incidents of which 160 happened during operation. According to PARLOC, full descriptions of all incidents are not available due to missing reported anonymous data. These statistics differ in other parts of the world, but nevertheless highlight the importance of offshore asset integrity, and the need to access the latest repair technology to respond when required.
During operation, damage can be caused by internal and external corrosion, hydrogen-induced stress cracking (HISC), environmental factors such as unstable seabed conditions or seismic related damage, and third-party impacts such as anchors and other dropped objects. The risk of damage depends on many factors, but typically includes the design of the pipeline, the environmental conditions, and the intensity of adjacent human activities. Additional logistical challenges also apply if the offshore repair operations involve isolating topsides on a production platform.
The extent of possible damage can vary from insignificant to a fully buckled or parted pipeline, and governs the repair preparedness strategy. For extensive damage of large sections of the pipeline, repair options are usually limited to cut and replacement using hot tap and bypass technology with substantial opex implications due to lost production time. For most local damage, such as external or internal corrosion and mechanical damage on a local scale (i.e. dents, wrinkles, buckles or girth weld defects), repair methods that involve minimal or no lost production time can be viable. These repair methods are collectively referred to as “live” repair.
Most subsea pipeline repair technologies involve fittings that can be connected to the pipeline via mechanical means, such as couplings, clamps, T-branch connections, or by welding. Isolation plugs are used to limit emptying volume of internal fluid and sea water filling of the pipeline during the repair. Offshore repairs can also be challenging and costly in terms of logistics. Most shallow-water repairs (down to 180 m/591 ft water depth in Norwegian waters) have historically been performed by divers. In deeper waters, pipeline repairs have to be conducted via remotely controlled technologies. Qualification of such technologies and equipment requires in-depth knowledge of the pipeline design parameters and operational experience. To date, there are very few options for deep and ultra-deepwater pipeline repair.
DNV GL has served as an independent technical advisor on several pipeline repair projects in the past few decades, to enable “live” pipeline repair without compromising on safety and integrity. The company has developed a number of practical repair procedures and a range of “live” repair solutions. These include plugging and grouted repair clamps for pipelines, and in-service welding of split-sleeves and stand-off sleeves with internal gas containment for repairs on leaking lines, grouted sleeves, and tees for pipelines.
Responsible for 170 world leading offshore standards and recommended practices (RPs), DNV GL is currently updating one of its leading RPs for offshore pipeline repair – DNV-RP-F113 – through a fasttrack joint industry project (JIP). The RP is widely referenced for the qualification of fittings and systems used for pipeline subsea repair and/or modifications and tie-ins. The guidelines include aspects relating to the design, manufacture, installation, and operation of such fittings and systems. However, the latest version of this RP was published eight years ago and a number of new technologies have been developed since then. This new JIP aims to capture the latest best practices, experiences, and expertise from the main providers and operators of pipeline repair equipment and tools, and to formalize pipeline subsea repair criteria and procedures into an internationally recognized standard.
The new edition of the RP will be harmonized with the latest revision of the Offshore Standard, DNV-OS-F101, on subsea pipelines, and will extend coverage to repair of clad and lined pipe, surface pipeline recovery, damage assessment, including root cause assessments, inspection methods, criticality assessment, selection of mitigations and repair methods for given damage levels, and lifecycle management of pipeline repair operations.
The new edition will also provide more guidelines on the safety (including topside and landfall) and barrier philosophy related to offshore pipeline repairs, and will provide further assistance on considerations for post-lay ovality of the pipe, and test requirements after the repair operation.
Other improved design and qualification guidelines will relate to pipeline isolation plugs; sour service; high temperature/high pressure (HT/HP) pipeline repair; the lifetime performance of elastomeric seals; and acceptance criteria for possible effects on the pipeline surface from coating removal tools. It will also address updated guidelines and acceptance criteria on hyperbaric welding, burst capacity check for welding on in-service pipelines, and installation aspects such as longitudinal seam weld removal.
未经允许,不得转载本站任何文章: